Precision Perfect - Inside BAC's efforts to bolster the steelmaking furnaces at ArcelorMittal’s Burns Harbor
Strategically situated on Lake Michigan in Northwest Indiana, 50 miles southeast of Chicago, sits Burns Harbor, ArcelorMittal’s second largest steel making facility in the country. The fully integrated plant’s location—bordered on both sides by a national park—affords prime shipping access to the Port of Indiana, as well as convenient highway and railroad access to the rest of the country.
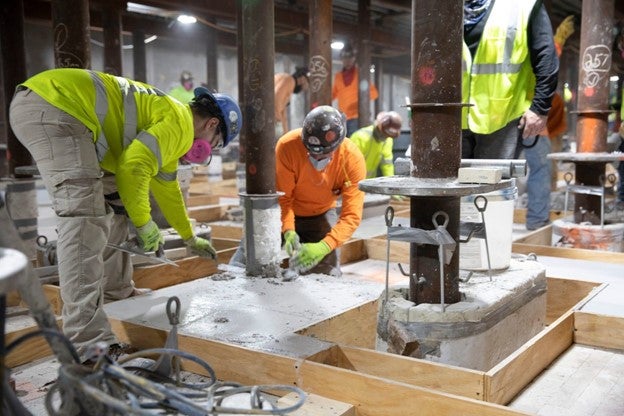
The facility’s strategic advantage is that it operates two blast furnaces capable of producing five million tons of raw steel annually—a payload that’s critical to serving the automotive industry, as well as the appliance, construction, converters, distribution, and pipe and tube markets.
As part of its Action 2020 Improvement Plan, ArcelorMittal invested $140 million into building two of the world’s largest walking beam reheat furnaces—the facility’s No. 4 and 5 furnaces located at its 80-inch Hot Strip Mill. The furnaces, which were added to improve surface quality and production, are capable of producing 500 tons each per hour, a 40% increase in productivity. In layman’s terms, the new furnaces “walk” the slabs instead of pushing them through the reheat furnaces, thus eliminating surface defects.
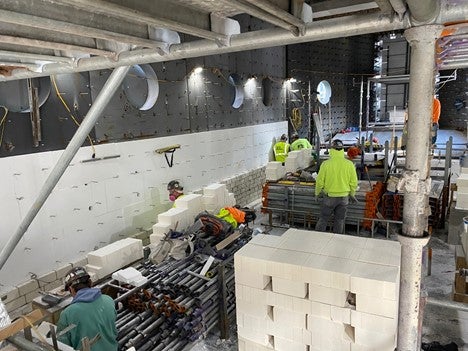
At the center of ArcelorMittal’s plan was BAC signatory contractor Barton Malow, which was awarded the refractory work through general contractor Graycor. The scope of Barton Malow’s work included the refractory installation of the two furnaces (each was approximately 210 feet in length and 15 feet high), the waste gas duct and heat recuperators, and the dual 217-foot stacks, which are lined with refractory.
“The architectural design was challenging,” recalls Barton Malow’s Superintendent Brian Mielczarek, a 22-year member of BAC Local 4 IN/KY. “I believe this is the first of its kind in the States. Everything was segmented, checkerboarded into small segments with firebreaks built into them to allow for better expansion and contraction of the materials to make them last longer.”
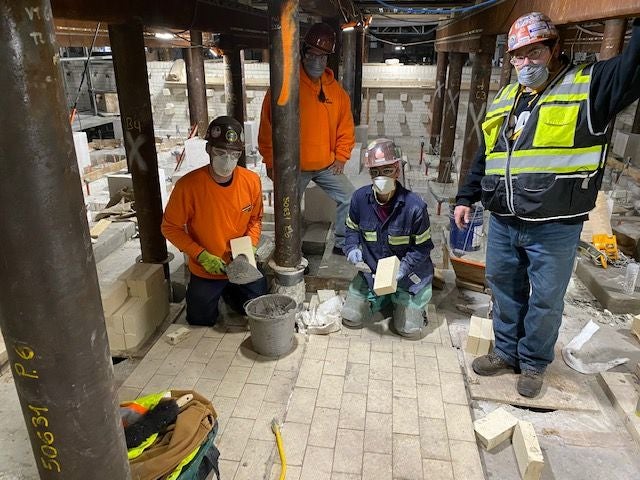
For some perspective on the scope of materials BAC members used on the Burns Harbor job, there were 308 tons of insulation and hard/dense fire bricks; 602 tons of refractory castables; 544 tons of fiber blanket modules and insulating boards; 2,800 pieces of pre-manufactured pipe shapes; and 260 tons of gunite.
To make things even more interesting, Mielczarek says nothing was continuous from the floor to the walls and roof. For example, one stack had more than 3,000 segments in it. In addition, moving the material into all the different areas posed its share of challenges.
But before the Barton Malow team could even tackle those challenges, the threat posed by the COVID-19 pandemic had to be addressed. From Day 1 in March, Barton Malow in coordination with Local 4 not only navigated the complicated and intricate pieces of the job, they were also vigilant about members’ safety and health, including the requirement for wearing face masks across the project.
At peak of the job, Barton Malow employed 75 Local 4 bricklayers on the job. “This was an obvious daily challenge to coordinate the manpower and deal with daily issues in the middle of a pandemic,” says Local 4 Steward Brian Collins. “I believe that Local 4 and Barton Malow are a great example of a partnership that has been tried with a project of this size in the middle of a pandemic. I’m proud of our membership with respect to their professionalism, ability to adapt and their skill set to figure this project out.”
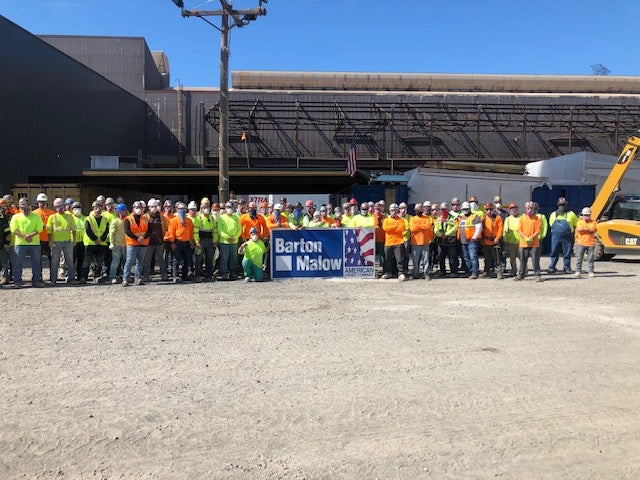
As any BAC Contractor will admit, manning a project of this size with local craftsworkers is always a challenge. Every step is critical—from getting the steward on the job, to recruiting local general foreman, and keeping the apprentice ratio in balance. In addition, as local general foreman and foremen start reading prints and devising a work plan, they must build their crews.
All this in a pandemic.
“Having local bricklayers in high level management positions always gives us the upper hand regarding work assignments and this project was a great example of that,” says President of Local 4 IN/KY Steve Knowles.
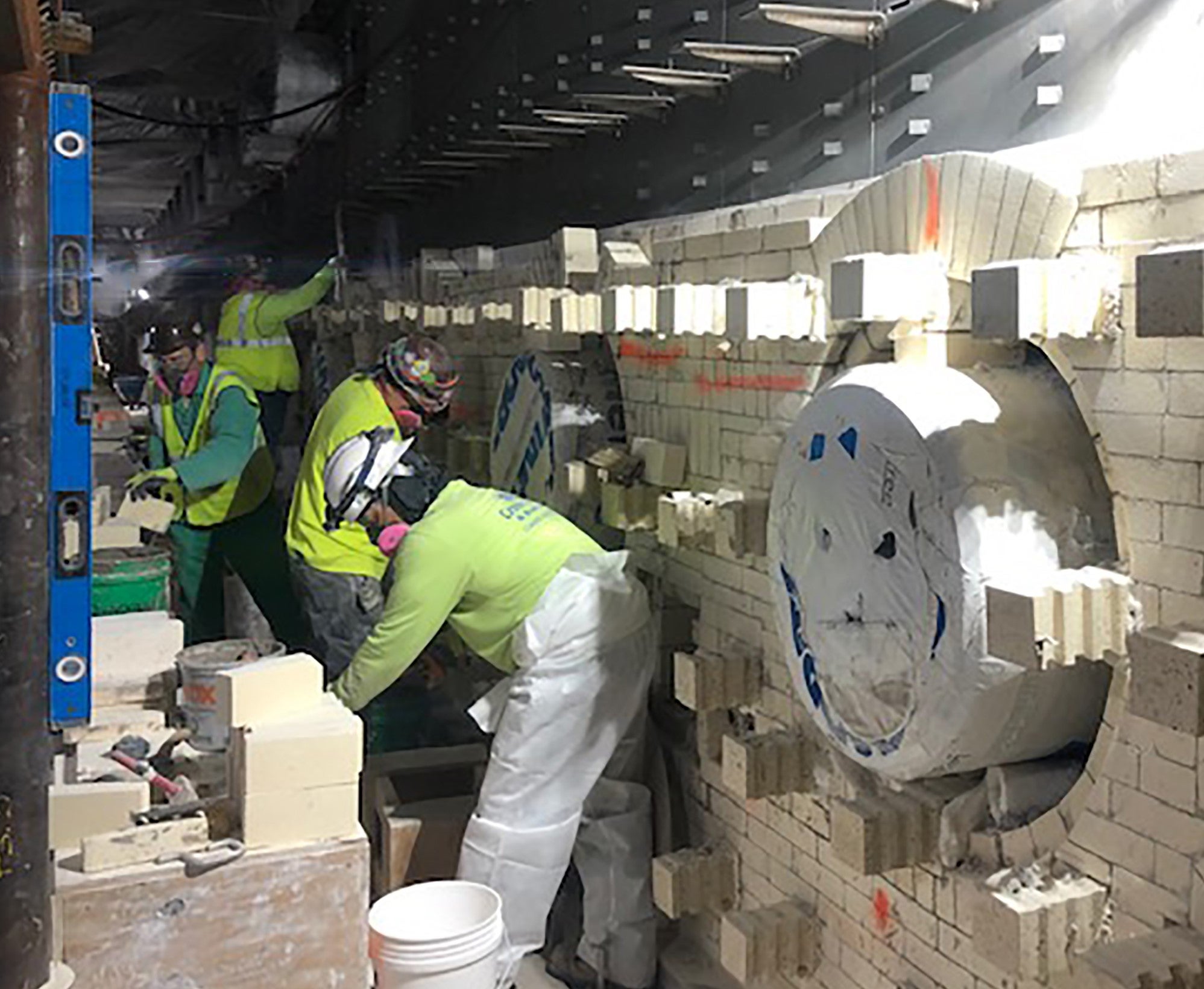
Communication was another critical component of BAC Local 4 IN/KY’s success, led by steward Brian Collins and the local superintendent, general foreman and foremen, all the way up to Barton Malow corporate. “COVID-19 is something no one could have anticipated or prepared for, so we had to work together from every member on-site all the way up through Barton Malow Management,” says Jeremy Rivas, Field Representative for BAC Local 4 IN/KY.
As with any job, the success of the final product is something that everyone involved can walk away with. “It’s been an honor and a pleasure to have worked and supervised the guniting of these furnaces and stacks,” says Foreman Darren Stout. “This is the absolute best work I’ve been involved with in both furnaces and stacks, and I’ve been doing this for 27 years. I like to describe this work as sculptured brilliance.”
BAC Local 4 IN/KY member Shannon Szelinski says it is amazing to see a project like this up close. “There was a lot of intricate brick work, which was not only challenging for our foreman, but for a good portion of bricklayers who might not have ever seen this type of work. The foremen did a great job figuring out the blueprints and putting together a plan.”
In the end, it was BAC’s creativity and execution that made the difference. “This project tested Local 4’s skill set and leadership,” Mielczarek says. “I believe we all answered the call on this once-in-a-lifetime project.”