The Importance of Properly Fitting Personal Protective Equipment (PPE)
How many times do you go to grab Personal Protective Equipment (PPE) when on a jobsite? When you need a harness, do you find one that fits you correctly, or do you just grab whatever’s available? Are you adjusting the harness to fit properly? Are the gloves you’re provided with too tight or too loose? These are important questions you need to consider as you select your PPE for the task at hand.
Personal protective equipment is the last line of defense against potential hazards, so it’s crucial that it fits correctly. When PPE does not fit, it can lead to a range of problems. Loose-fitting gear can become a snag hazard, increasing the risk of accidents, while equipment that is too tight can restrict movement and impair your ability to perform your job effectively. It can also lead to physical discomfort, distraction, and fatigue – disrupting focus and compromising alertness on the job site.
For example, harness straps around your thighs should be snug but not constricting, and you should be able to fit a couple of fingers between the webbing and your body. The same goes for the torso straps; if these straps are too loose or too tight a worker could slip out, leading to serious injury.
Training and Communication
It’s crucial that workers undergo the proper training on how to use and maintain PPE. Many workers may not know how to adjust their equipment for a snug fit or how to identify the right size. Training sessions that cover these topics can empower workers to take ownership of their safety. Additionally, open lines of communication with the contractor and with the union regarding PPE issues can help create a safer environment.
The Shift Towards Proper Fit: New OSHA Regulations
On December 11, 2024, the Occupational Safety and Health Administration (OSHA) announced a final rule requiring construction employers to provide PPE that “properly fits” each employee. This means employers must ensure PPE is appropriately sized for each worker. The rule went into effect on January 13, 2025, marking a significant step towards enhancing workplace safety.
This regulation not only emphasizes the importance of proper fit but also highlights the responsibility of employers to prioritize the safety and well-being of their workforce. Workers deserve to have equipment tailored to their individual needs, as ill-fitting PPE compromises safety in the line of duty.
The Bottom Line: Safety is Personal
Personal Protective Equipment – emphasis on “personal” – must fit each worker properly. This is not just a guideline, it’s a critical aspect of workplace safety that can mean the difference between life and death. Every worker has unique body shapes and sizes, and that individuality must be considered when selecting PPE.
While regulations like those from OSHA are essential, safety ultimately begins with us as individuals. It is our responsibility to speak up if our equipment does not fit right. If something feels off – whether a helmet doesn’t sit securely, or gloves make it difficult to grip tools – we must communicate those concerns to our supervisors or safety officers.
Advocating for the right fit does not just benefit us, it sets a precedent for our coworkers as well. When we prioritize our safety, we encourage a culture of vigilance and care in our workplaces. This not only protects individuals but also strengthens the entire team.
Fighting for federal and state regulations is only one aspect of a union safety program. A larger part is working together on the jobsite to create a culture where every worker feels valued and protected. Every time you put on your PPE, take a moment to ensure it fits right. It’s an investment in your future.
Editor’s Note
As this issue goes to press, the Department of Labor under the Trump administration is reviewing many of the rules put in place by the Biden administration, including the PPE Fit rule discussed in this article. We will update on any rule changes in following issues of the BAC Journal as well as on our website, bacweb.org/safety.
Climbing the Rungs of Ladder Safety
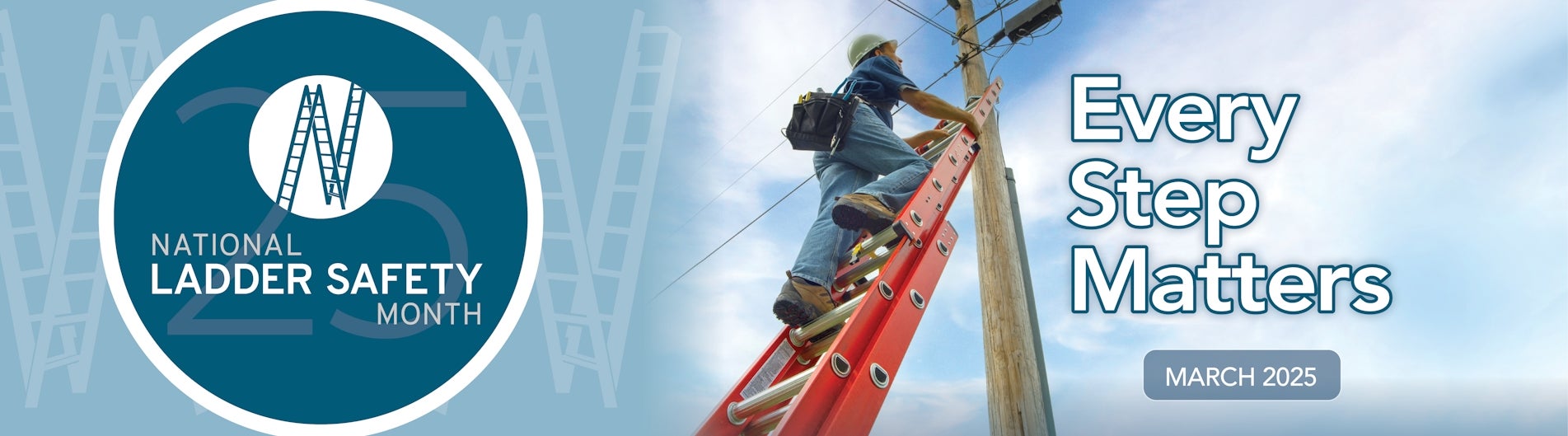
In recognition of March as Ladder Safety Month, the BAC joined forces again with the American Ladder Institute to elevate awareness about best practices in ladder use.
Through this collaborative initiative, both organizations committed to educating construction workers and homeowners alike on proper ladder selection, maintenance, and safe operation techniques. In a demonstration of our commitment to safety, the BAC, in partnership with the International Masonry Institute, supported enhanced safety training programs.
Throughout March, our partners at the American Ladder Institute, working alongside safety initiatives from the BAC, will focus on key themes including Training and Awareness, Inspection and Maintenance, Stabilization, Setup, Accessories, Safe Climbing, and Positioning. As part of this comprehensive safety campaign, the BAC has proudly sponsored the Ladder Institute’s webinar series that addresses topics such as Common Ladder Accidents and How to Avoid Them, effective Ladder Safety Set-Up and Tips, as well as DIY and Homeowner Ladder Safety strategies. BAC also pushed specific ladder safety toolbox talks to be reviewed across North America.
Ladder related accidents happen to tens of thousands of construction workers every year, with over 100 fatalities – with likely thousands more not reported. Over half of the ladders involved in the workplace accident were not inspected before use. Take a few minutes each day to make sure you are selecting the correct ladder for the job, and it is set up properly.
We encourage all who are interested to explore our own series of safety webinars, available at bacweb.org/safety. For further training resources, including specific guidance on ladder safety, please visit www.laddersafetytraining.org.