Timeless Masonry with a New Technological Assist
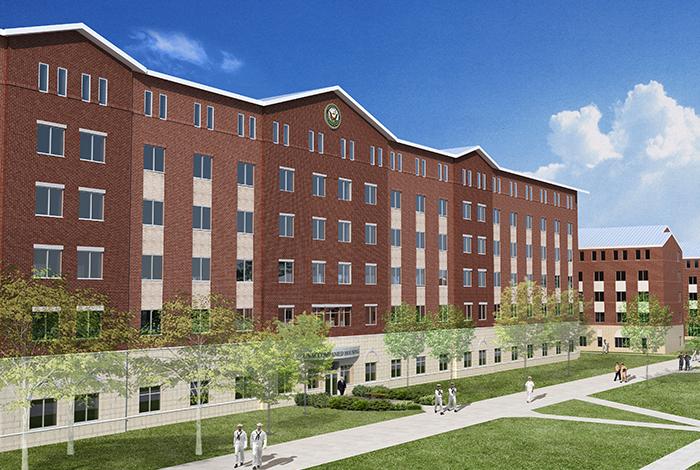
Thirty-two members of BAC Local 21 Illinois, including five apprentices, are busy working to complete a 166,000-square-foot barracks at the Naval Station Great Lakes, the Navy’s largest training installation and home of the Navy’s only Boot Camp, located north of Chicago. The six-story project, known as P-714 Unaccompanied Housing Project, will consist of reinforced concrete foundation with a brick and cast-stone exterior and will house 616 enlisted military personnel when completed in late 2020.
BAC contractor Jimmy-Z Masonry of Crystal Lake, Illinois is the mason contractor on this impressive project that features six stories of masonry veneer with CMU back-up, and nearly 70,000 square feet of CMU partition walls throughout the project. The exterior veneer is comprised of 53,000 square feet of Sioux City Red utility brick laid in a One-Third Bond and 18,000 square feet of Arriscraft Renaissance cast stone units. BAC members are installing all facets of the masonry wall system on this project including all necessary air barrier, flashing, fire-stop, and caulking.
CMU backup for the exterior veneer, including 11,000 12” x 8” x 16” CMU, 13,000 8” x 8” x 16” CMU, and over 57,000 8” x 8” x 32” CMU specially-designed for this project, are being laid by BAC bricklayers using the MULE (Material Unit Lift Enhancer). At its peak, this project had 12 MULEs working across the site, the largest number of MULEs in North America operating on a single construction site.

The MULE, developed by Construction Robotics, is designed to make material lifting nearly weightless, allowing masons to handle the 70 lb. 32” CMU and conventional 12” CMU while reducing fatigue and injuries. The MULE was also used to good effect in setting the 80 lb. 4” x 12” x 24” Arriscraft cast stone units.
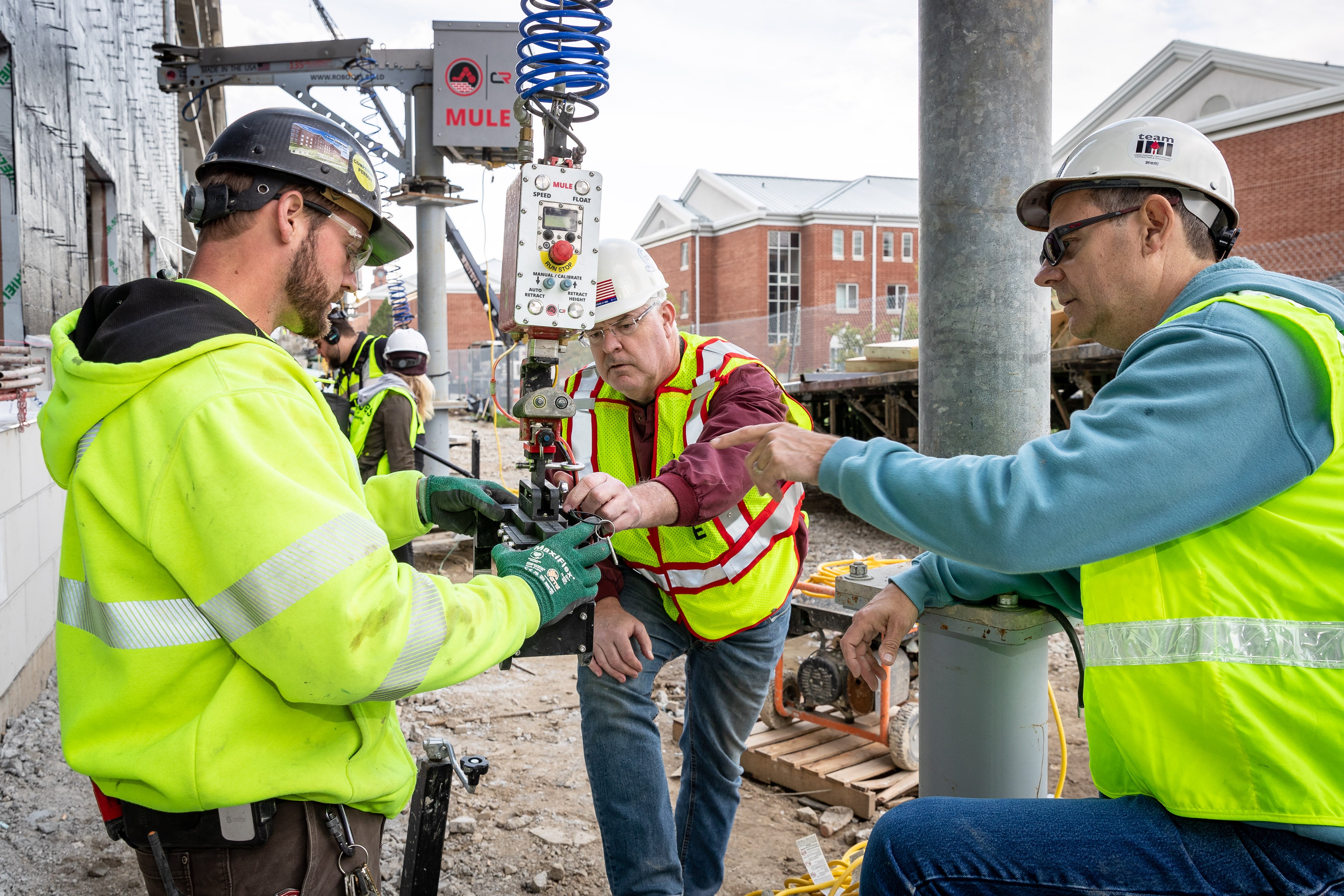
BAC Local 21 member and foreman for Jimmy Z Masonry, Zack Zuidema, said that “Masons are quick to adapt to the capabilities of the MULE. It doesn’t displace the bricklayer because you still need the skills and knowledge that the mason brings to the job. And it makes the jobsite safer and more productive.”
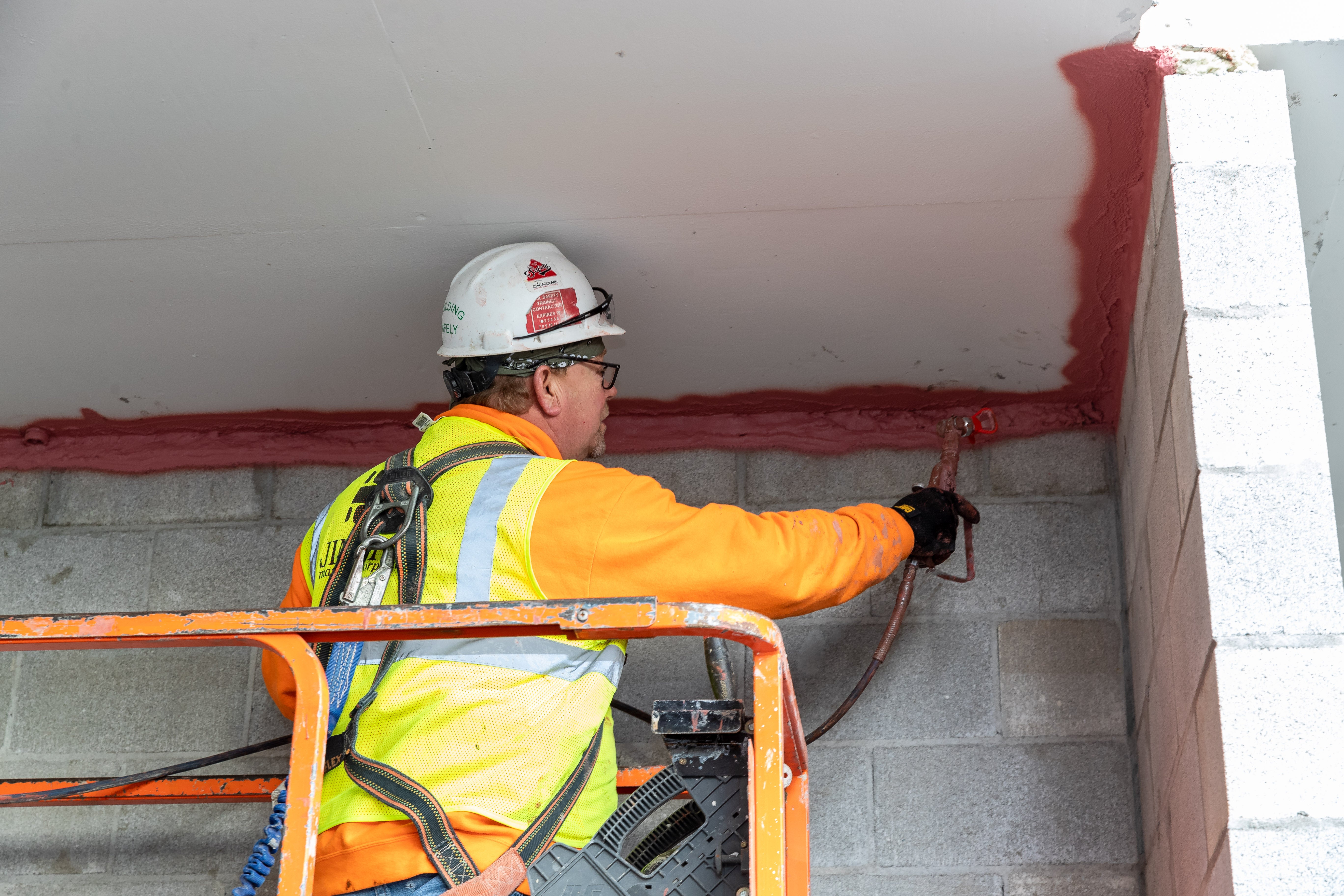
That is a sentiment echoed by Jim Allen, President of the BAC Administrative District Council 1 of Illinois (ADC 1 of IL). “The District Council recognized that when a new technology enters the marketplace, BAC needs to be positioned to claim that work. Consequently, we coordinated with our JATC to acquire the shared use of a MULE and offer training to BAC members and signatory contractors to ensure that BAC members reap the benefits of this technology.”
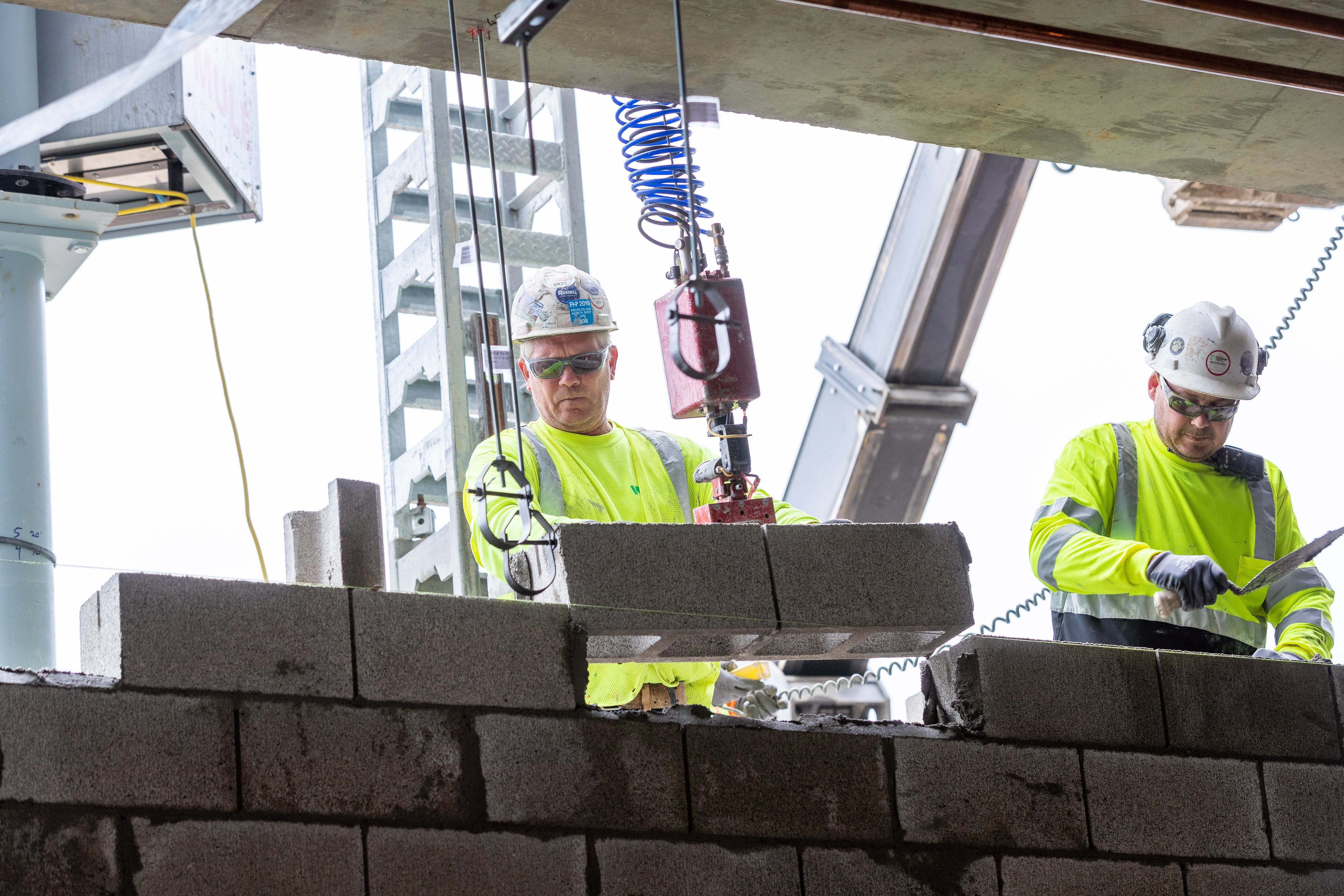
IMTEF National Training Director Bob Arnold recognized the potential impact of the MULE when he first encountered it several years ago and was instrumental in ensuring that the National Training Center obtained a MULE to be at the forefront of training efforts for BAC members. Says Arnold, “While the MULE can’t replace a bricklayer, it can enhance and extend careers in our trade on those projects where a MULE is appropriate. If the MULE has a place in our industry, BAC will be on the scene to see that it is used safely and effectively.” Indeed, Arnold and his team at IMTEF have been central to developing the training modules for MULE in coordination with Construction Robotics.
IU Secretary-Treasurer Tim Driscoll sees a potential role for this technology in the masonry industry. “The MULE is necessarily limited in its scope and application by both building design and site coordination. But where it is viable, it can assist the bricklayer in producing the quality and quantity of masonry needed to ensure that masonry walls remain the best value in the construction industry, while also helping to reduce the strain and injuries that are prevalent across our trade. Anything that makes masonry materials more competitive in today’s marketplace and has the potential to produce more man-hours cannot be ignored,” Driscoll said.